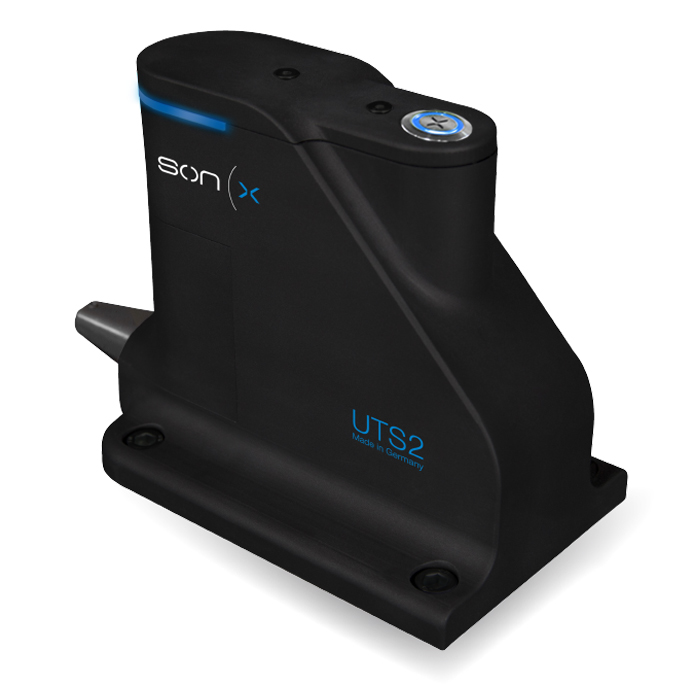
Overview
THE ULTRASONIC TOOLING SYSTEM
The new 100 kHz ultrasonic system UTS2 from son-x GmbH enables direct ultra-precision machining of steel with no geometric restrictions. The UTS2 operates at a unique frequency of 100 kHz, so that maximum efficiency is combined with precision. With the innovative process, steel alloys and some types of glass can be manufactured with the highest quality (Ra <3nm, PV <200 nm). The classic application is the optical mold.
THE TECHNOLOGY
The UTS2 works with the principle of ultrasonic-assisted machining. In this case, the diamond tool is set into a linear oscillatory motion in the cutting direction at a frequency of 100 000 Hz.
The high-frequency vibration of the tool causes a repeated separation of the cutting tool and the material. The contact time between diamond and material is only about 2 µs per cycle and overall 20% of the total processing time. The cyclical tool contact is repeated 100 000 times per second.
A large number of positive effects are achieved using this technology, e.g. improved cooling conditions and the interception of chemical wear reactions. This significantly reduces the wear of the diamond and enables the direct cutting of stainless steel.
The new 100 kHz ultrasonic system UTS2 from son-x GmbH enables direct ultra-precision machining of steel with no geometric restrictions. The UTS2 operates at a unique frequency of 100 kHz, so that maximum efficiency is combined with precision. With the innovative process, steel alloys and some types of glass can be manufactured with the highest quality (Ra <3nm, PV <200 nm). The classic application is the optical mold.
THE TECHNOLOGY
The UTS2 works with the principle of ultrasonic-assisted machining. In this case, the diamond tool is set into a linear oscillatory motion in the cutting direction at a frequency of 100 000 Hz.
The high-frequency vibration of the tool causes a repeated separation of the cutting tool and the material. The contact time between diamond and material is only about 2 µs per cycle and overall 20% of the total processing time. The cyclical tool contact is repeated 100 000 times per second.
A large number of positive effects are achieved using this technology, e.g. improved cooling conditions and the interception of chemical wear reactions. This significantly reduces the wear of the diamond and enables the direct cutting of stainless steel.
Vibration frequency | 100 000Hz |
Vibration amplitude | 0.1-2μm |
Dimensions of the tool holder width/depth/height | 79/160/107(mm) |
Dimensions of the ultrasound generator width/depth/height |
365/390/135(mm) |
Weight of the tool holder | 1.2kg |
Tool overhang(geometrical freedom in Z) | >50mm(variable on demand) |
Tool height above the base plate | 16mm(variable on demand) |
Electrical requirements | 110-220V, <5A, 50-60Hz |
Power consumption/strong | average 200 Watt |
Recommended lubrication | Spray mist |
Additional system cooling | Not required |
Option | Microheight adjustment unit or adapter plate |
Typical roughness Ra | ~3nm |
Typical shape accuracy PV | <200nm |
With the UTS2, all the benefits of ultra-precision machining are transferred to various materials which previously couldn’t be processed using diamonds. As a result, several new applications for processing arise.
1.AUTOMOTIVE
LED headlights in automobiles have complex geometries for selective light focusing. Using UTS2 to manufacture optical mold inserts with microstructured freeform surfaces directly in hardened steel alloys, for which our total competency is required.
2.LED LIGHTING
Made of steel, our mold inserts for the processing of plastics and silicones which require high temperatures and forces in injection molding, have an above-average service life.
3.CONTACT LENSES
UTS2 could be used for the production of contact lenses with spherical, aspherical and toric geometries.
4.OPTICS
UTS2 could be applied in production of mirror optics and prototypes, as well as the manufacturing of mold inserts for injection molding of imaging optics.
1.AUTOMOTIVE
LED headlights in automobiles have complex geometries for selective light focusing. Using UTS2 to manufacture optical mold inserts with microstructured freeform surfaces directly in hardened steel alloys, for which our total competency is required.
2.LED LIGHTING
Made of steel, our mold inserts for the processing of plastics and silicones which require high temperatures and forces in injection molding, have an above-average service life.
3.CONTACT LENSES
UTS2 could be used for the production of contact lenses with spherical, aspherical and toric geometries.
4.OPTICS
UTS2 could be applied in production of mirror optics and prototypes, as well as the manufacturing of mold inserts for injection molding of imaging optics.
Specification
Vibration frequency | 100 000Hz |
Vibration amplitude | 0.1-2μm |
Dimensions of the tool holder width/depth/height | 79/160/107(mm) |
Dimensions of the ultrasound generator width/depth/height |
365/390/135(mm) |
Weight of the tool holder | 1.2kg |
Tool overhang(geometrical freedom in Z) | >50mm(variable on demand) |
Tool height above the base plate | 16mm(variable on demand) |
Electrical requirements | 110-220V, <5A, 50-60Hz |
Power consumption/strong | average 200 Watt |
Recommended lubrication | Spray mist |
Additional system cooling | Not required |
Option | Microheight adjustment unit or adapter plate |
Typical roughness Ra | ~3nm |
Typical shape accuracy PV | <200nm |
Applications
With the UTS2, all the benefits of ultra-precision machining are transferred to various materials which previously couldn’t be processed using diamonds. As a result, several new applications for processing arise.
1.AUTOMOTIVE
LED headlights in automobiles have complex geometries for selective light focusing. Using UTS2 to manufacture optical mold inserts with microstructured freeform surfaces directly in hardened steel alloys, for which our total competency is required.
2.LED LIGHTING
Made of steel, our mold inserts for the processing of plastics and silicones which require high temperatures and forces in injection molding, have an above-average service life.
3.CONTACT LENSES
UTS2 could be used for the production of contact lenses with spherical, aspherical and toric geometries.
4.OPTICS
UTS2 could be applied in production of mirror optics and prototypes, as well as the manufacturing of mold inserts for injection molding of imaging optics.
1.AUTOMOTIVE
LED headlights in automobiles have complex geometries for selective light focusing. Using UTS2 to manufacture optical mold inserts with microstructured freeform surfaces directly in hardened steel alloys, for which our total competency is required.
2.LED LIGHTING
Made of steel, our mold inserts for the processing of plastics and silicones which require high temperatures and forces in injection molding, have an above-average service life.
3.CONTACT LENSES
UTS2 could be used for the production of contact lenses with spherical, aspherical and toric geometries.
4.OPTICS
UTS2 could be applied in production of mirror optics and prototypes, as well as the manufacturing of mold inserts for injection molding of imaging optics.